- The Formula F1x
- Posts
- Deep Dive: Aerodynamic Testing in Formula 1
Deep Dive: Aerodynamic Testing in Formula 1
Aerodynamic Testing in Formula 1: Precision Engineering for Peak Performance
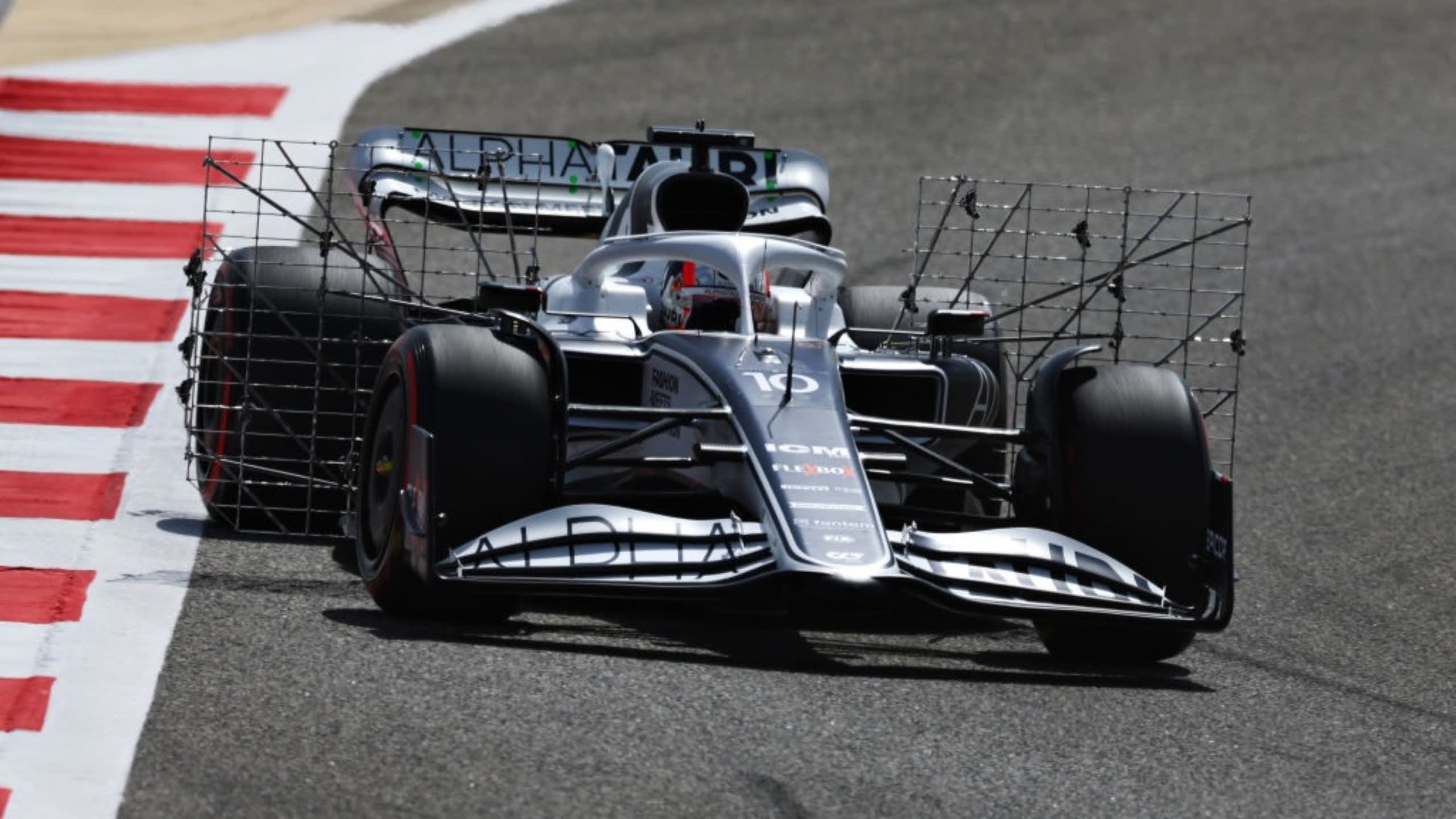
Aerodynamics is one of the most critical aspects of Formula 1 car design, influencing speed, cornering, and overall performance. To gain a competitive edge, teams invest heavily in aerodynamic testing, employing state-of-the-art facilities and advanced simulation tools. This essay explores what aerodynamic testing is like in Formula 1, the techniques and equipment used, the data teams gather, and the impact of these innovations on the sport.
What is Aerodynamic Testing?
Aerodynamic testing in Formula 1 involves analyzing how air flows around the car to optimize performance. This includes assessing drag (air resistance), downforce (air pressure pushing the car onto the track), and airflow efficiency through various car components like wings, side pods, and underbody. By refining these factors, teams can create a car that balances speed and stability across different track conditions.
Testing is conducted through two primary methods:
Wind Tunnel Testing: Physical models or full-size cars are tested in controlled environments using powerful wind machines.
Computational Fluid Dynamics (CFD): Virtual simulations analyze airflow digitally.
Do Teams Use Full-Size Cars?
In most cases, Formula 1 teams do not use full-size cars for wind tunnel testing. Instead, regulations set by the FIA limit teams to using 60% scale models to maintain cost control and fairness. These scale models are highly detailed replicas of the actual car, complete with functional wings, suspension systems, and other aerodynamic features.
However, some testing, particularly in Computational Fluid Dynamics, uses full-size car data. On-track testing during practice sessions also helps validate results from wind tunnels and simulations.
What Are Teams Looking For?
Aerodynamic testing is focused on multiple objectives:
Minimizing Drag: Reducing air resistance to maximize straight-line speed.
Maximizing Downforce: Increasing grip for better cornering and stability.
Balancing Front and Rear Airflow: Achieving optimal handling by balancing aerodynamic forces across the car.
Cooling Efficiency: Ensuring adequate airflow to cool the engine, brakes, and electronics.
Track-Specific Adjustments: Fine-tuning designs to suit specific tracks, such as high-downforce setups for Monaco or low-drag configurations for Monza.
Teams also analyze how turbulent air, often called "dirty air," affects the car's performance, especially during close racing conditions.
Testing Air from Different Directions
To replicate real-world conditions, wind tunnels can simulate air coming from various directions. This is crucial because on-track airflow is rarely uniform, with variables like crosswinds, turbulence from other cars, and track-specific elevation changes. Some wind tunnels can pivot the model or redirect airflow to mimic cornering scenarios or specific track features.
Teams also create digital models of racetracks to analyze how their cars will perform under actual race conditions. CFD simulations provide detailed insights into how air behaves across the car during acceleration, braking, and cornering.
The Machines Behind Wind Tunnel Testing
Wind tunnels are massive structures, often spanning several stories in height and requiring enormous amounts of energy to operate. Key components include:
Fans: Large industrial fans capable of generating wind speeds exceeding 300 km/h (186 mph), simulating the airflow a car experiences at race speed.
Rolling Roads: To mimic the movement of a car on a track, wind tunnels use rolling belts underneath the scale model. These systems replicate tire-road interactions.
Sensors and Probes: Advanced sensors collect data on pressure, airflow velocity, and force distribution across the car.
Costs of Wind Tunnel Testing
Building and maintaining a wind tunnel is an expensive endeavor. The construction cost of a high-quality wind tunnel ranges from $50 million to $100 million, depending on its complexity and capabilities. Operating these facilities adds significant costs, as they require vast amounts of electricity and specialized personnel to manage tests.
To reduce expenses, the FIA has imposed strict limits on wind tunnel usage. Teams are allowed a limited number of wind tunnel hours annually, encouraging efficiency and innovation in aerodynamic development.
Data Gathered from Aerodynamic Testing
Aerodynamic testing provides Formula 1 teams with a wealth of data, including:
Drag and Downforce Metrics: Precise measurements of air resistance and grip levels.
Pressure Distribution: Insights into how air pressure is distributed across different parts of the car.
Flow Visualization: Using tools like smoke or fluorescent paints to observe airflow patterns.
Energy Efficiency: Data on how airflow affects the car’s power unit and fuel consumption.
This information helps teams refine their designs, improving lap times and overall competitiveness.
Computational Fluid Dynamics (CFD)
CFD is an essential tool for modern Formula 1 teams, complementing wind tunnel testing. Using supercomputers, CFD creates virtual simulations of airflow, allowing engineers to test numerous configurations without building physical models. This method is especially useful for exploring innovative concepts and responding quickly to regulatory changes.
Interesting Facts About Aerodynamic Testing
Energy Consumption: Wind tunnels can consume as much energy in a single test session as several households use in a day.
CFD Revolution: In the 2000s, CFD became a game-changer for Formula 1, drastically reducing development time and costs.
Historic Shift: Before wind tunnels, teams relied on trial-and-error methods, testing cars directly on tracks without understanding the underlying airflow dynamics.
Banned Features: In the 2000s, loopholes in aerodynamic testing led to the creation of "double diffusers" and "F-ducts," which were later banned for giving unfair advantages.
Impact on Performance
Aerodynamic testing has a direct and profound impact on Formula 1 performance. Teams that excel in aerodynamics often dominate the sport, as seen with Red Bull Racing's mastery of downforce during their championship-winning years. In modern F1, even a small aerodynamic advantage can translate to tenths of a second per lap, which can be the difference between winning and losing.
Conclusion
Aerodynamic testing is a cornerstone of Formula 1 engineering, blending cutting-edge technology with rigorous analysis to optimize car performance. From wind tunnels to CFD simulations, teams employ sophisticated tools to unlock speed, stability, and efficiency. As Formula 1 continues to evolve, advancements in aerodynamic testing will remain central to the sport, pushing the boundaries of engineering and performance while ensuring cars deliver thrilling races for fans worldwide.
If you know anyone who may enjoy our content, please share our subscriber page to we can grow our community! https://theformulaf1x.beehiiv.com/subscribe